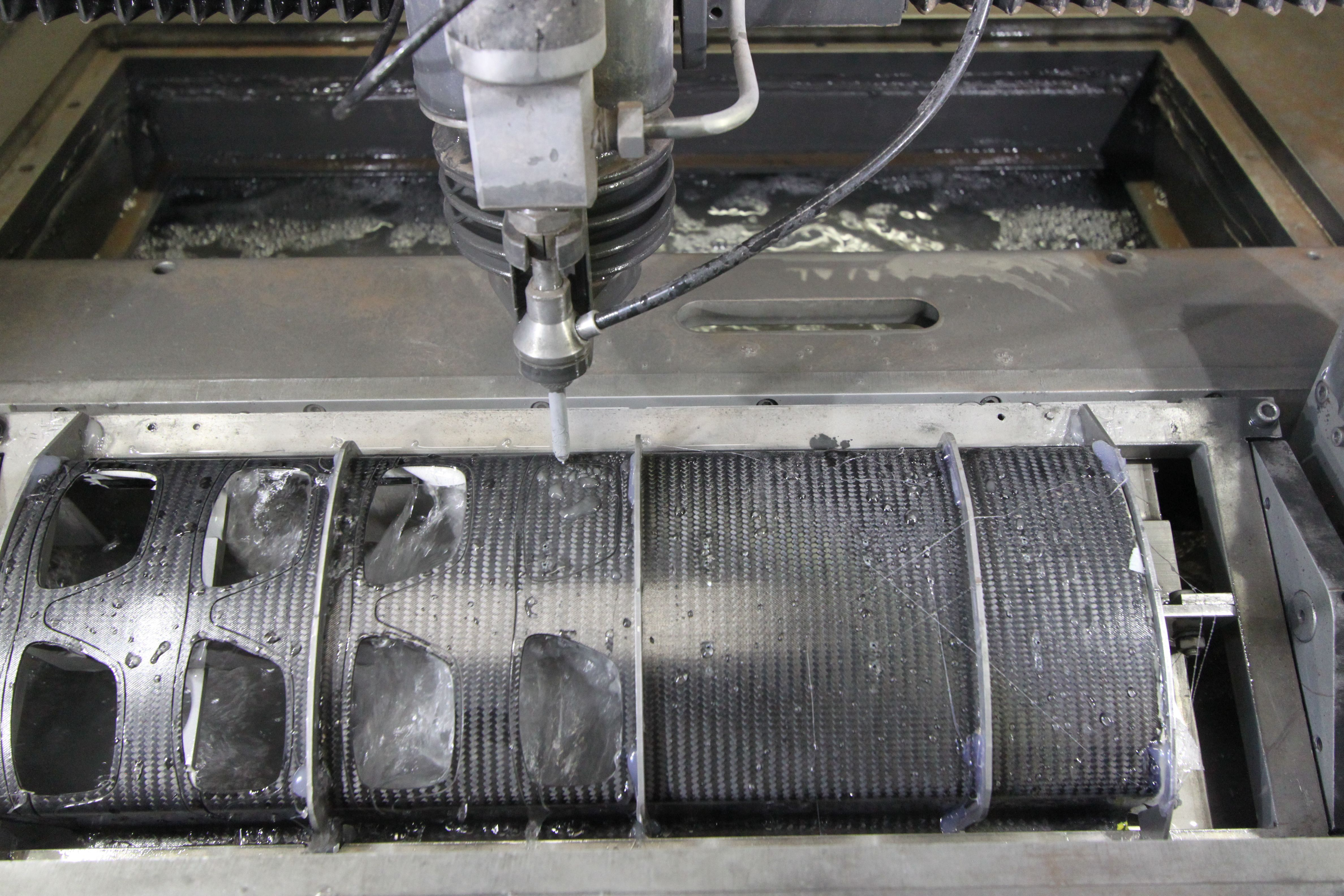
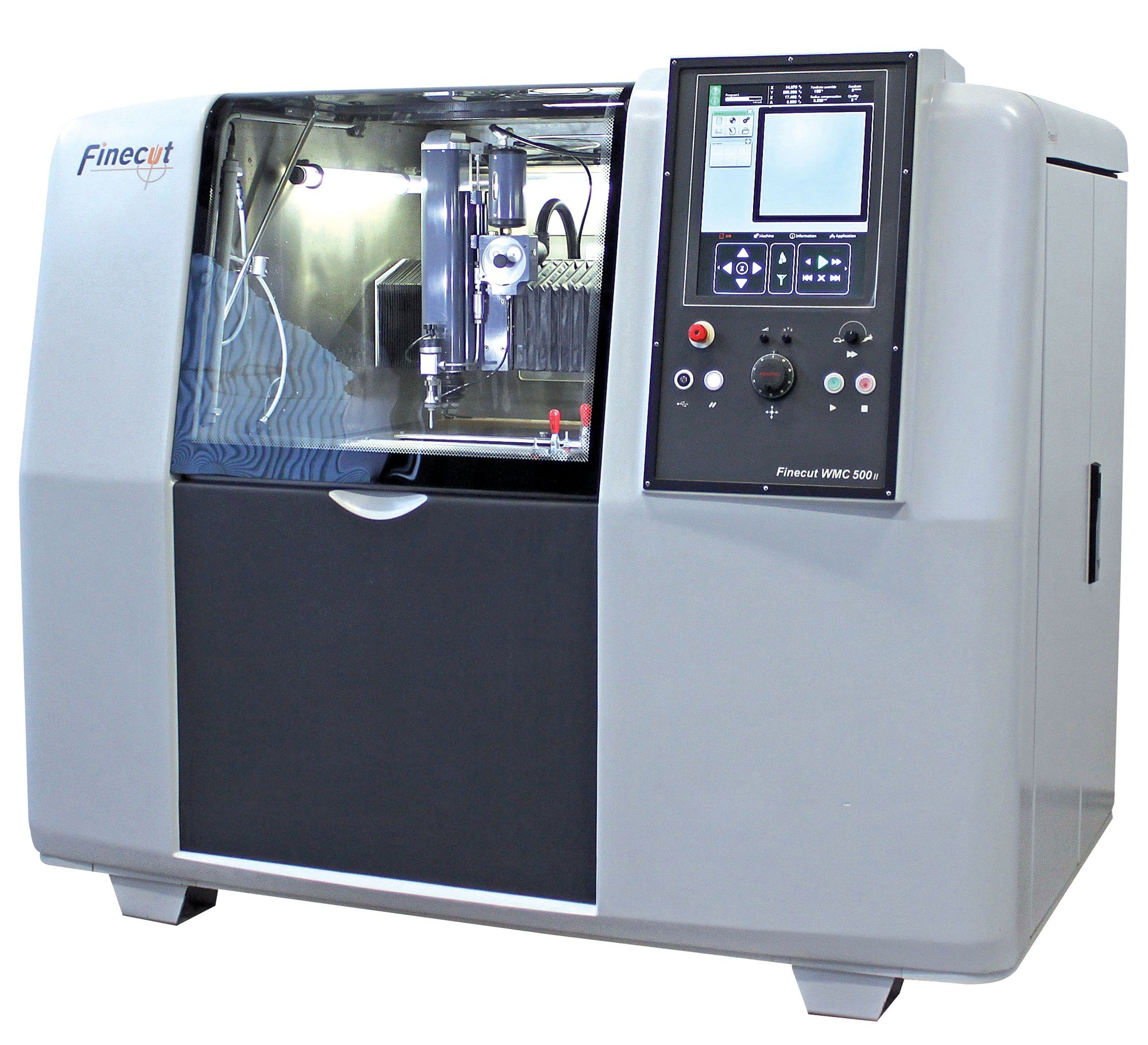
Abrasive waterjet machines have traditionally been regarded as inaccurate roughing machines requiring large amounts of space and huge water tanks. Thanks to developments in technology, Finepart’s 500mm x 500mm cutting table machine is not only compact, it is one of the most advanced pieces of equipment on the market.
Finepart’s next generation non-thermal micro abrasive waterjet machines are made with state-of-the-art components to provide the ultimate finish in precision cutting and their small footprint means they are suitable in any type of workshop environment. The absence of heat effect in the cutting process also makes them perfectly suited to industries such as medical and aerospace where heat affected zones are prohibited on certain components.
The benefits of a Finepart Waterjet Cutting Machines
Provide maximum flexibility in fine mechanics production
Available in 3, 4 and 5 axis
Increases cutting power considerably more than a pure waterjet
Can produce parts with a choice of rough separating cuts to precise taper-free cuts
Ultra-high precision cutting, with cutting speeds 10 times faster than wire-EDM Strong versatility - able to cut through virtually any material (hard materials such as wood and glass as well as soft materials like rubber or polymers) up to 30mm thick
5-axis machining enables the cutting of complex 3D shapes
No CNC skills required
Can lead to lower process costs
10x Cutting Speed Possible Compared to Wire-EDM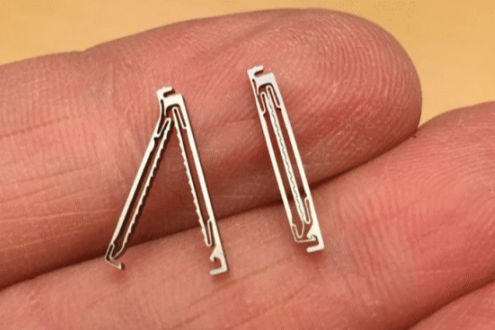
3 Axis
The Finecut Fine Abrasive Waterjet cutting system is the proprietary cutting system of Finepart. It was developed to accompany the Finecut Waterjet Machining Center and together they bring the waterjet technology to a whole new level of precision. The micro abrasive waterjet process is a particle erosion based, non-thermal cutting process. This process can cut virtually all materials, produces an excellent surface finish and does not change the material properties. Moreover, the process can pierce starting holes in the part and cut complex contours with minute features having radii down to 0.1 mm.
4-Axis
The 4-axis can be fitted with a work table plate on which any work piece can be placed. With this mechanism, the part can be re-oriented to provide access for cutting from different sides of the part. This motion system set up allows the jet nozzle to cut along a contour, following the part’s 3D curvature, moving all four axes in synchronous motion.The machine has a 5-axis controller with capability for tool center point programming. All these operations are easily programmed using the CAD/CAM software provided for the machine
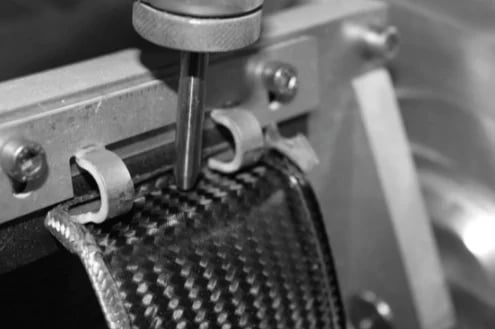
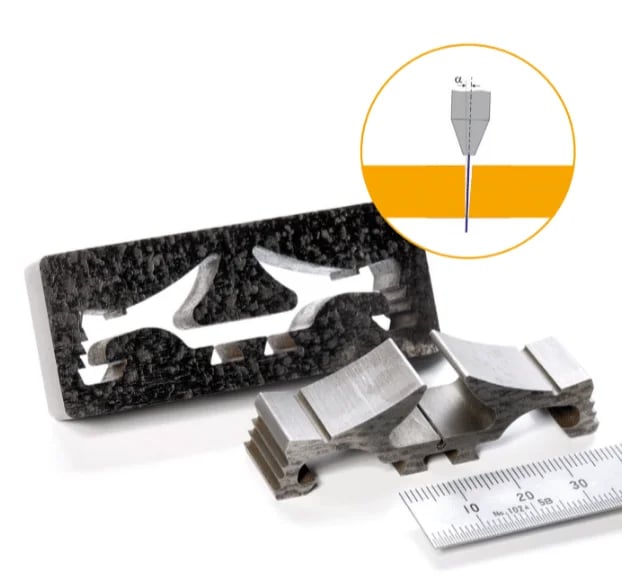
5 Axis ABX
With the ABX configuration the Finecut 5-axis waterjet machining center can cut 3D geometries with straight or slanted edges up to 15 degrees. This model enjoys the very high precision of the 3 axis Finecut machines with added capability to tilt the jet. By adding 5 axis capability, the jet can be tilted to cut oblique angles. Moreover, the taper in the cut can be compensated and speeds will not need to be reduced more than to meet an adequate surface quality. The jet angle adjustment can also avoid jet kick-back at lower part of inner corners. This is a time saver and brings you potential to significantly increase productivity which quickly returns its investment cost
5 Axis B4X
Our 5-axis motion systems can be used for slanting the cut surface in order to create 3D geometries, relief angles, or just to compensate for cut taper angle. With jet angle adjustments you can also avoid the jet kick-back at the lower part of sharp inner corners. All these functions are easily programmed using the CAD/CAM software provided for the machine. Our standard 5-axis type B4X facilitates 3D cutting up to ± 45°degrees on the part. The A-axis is table-mounted and moves the work piece. This means that the A-axis can rotate beyond ± 45°degrees if desired. The A-axis can alternatively be fitted with a chuck and used as arotary axis with full 360 degrees rotation, which enables cutting helical geometries as well as rotational symmetries.
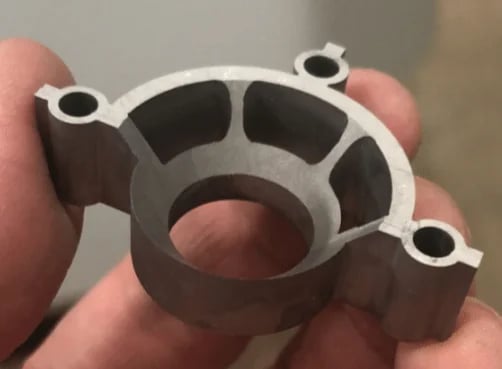
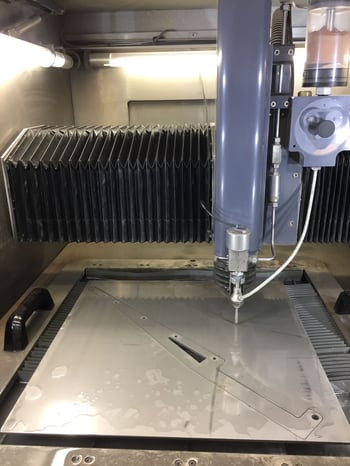
Why Choose Rainford?
Highly knowledgeable and experienced Finepart specialists
Create a reliable process for you, to match your expectations and fit your budget
Great communication and customer service
ISO 9001 certified
Why We Do What We Do
I would like to say thank you for your assistance so far. We have only drilled 4 x 0.80mm holes 50d deep but the fact they worked the first time was appreciated by everyone.
We use OSG mainly but when we have a specific job that needs doing, we come to Rainford Precision because they are and do the Crème De La Crème of Products and services.
The End Mill was an ideal choice due to the unusual shape and the need to have a small radius. They turned out great, and the surface finish is really good.
I would like to say thank you for the help you have given our project over the last few years. Your advice on the correct cutters plus the right speeds and feeds has not only helped with accuracy but brought the cycle times down so we can meet our project deadlines.
Thank you for making that so incredibly easy and prompt.
We received your delivery this morning as you had promised to do for us, thanks for that, it is great when a plan comes together.
A diamond service from Rainford as usual. The success of our company is very much down to the external support received from Key organisations such as Rainford Precision. Your company is one of the first I will always turn to assist us.
Book A Consultation
Revolutionise your machine drilling operations today! Take the first step by booking a consultation and a member of our seasoned team will analyse and optimise your processes, recommending cutting-edge technologies for enhanced precision and productivity.
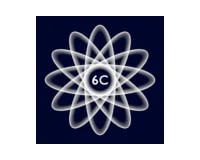
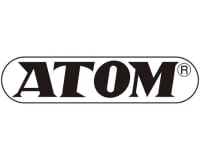
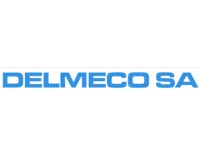
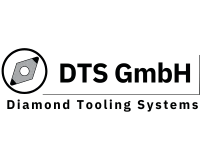
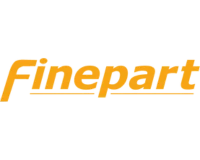
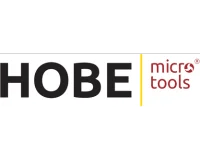
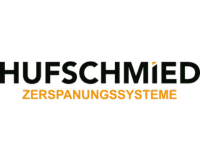
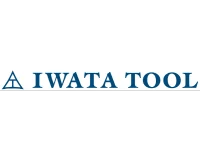
.png?width=2563&height=2351&name=KERN-Ametek-logo-rot-schwarz%20(1).png)
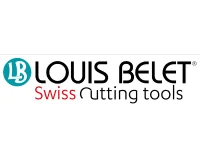
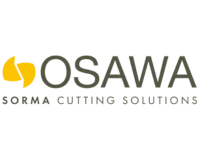
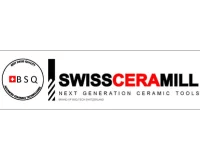
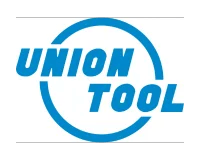
Interested In Our Products?
GET ACCESS TO OUR WIDE RANGE OF PRODUCT BROCHURES
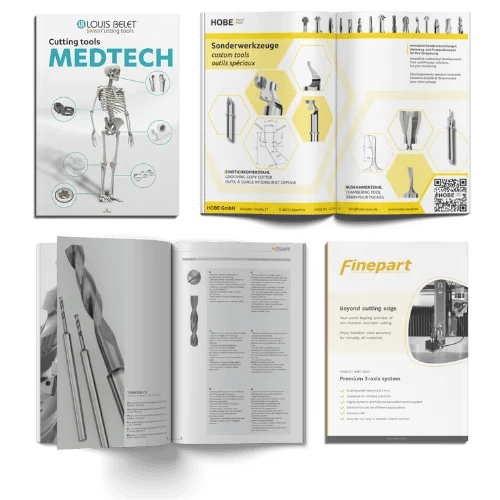
Latest From The Blog
4 min read
Advantages of Micro Abrasive Water Jet cutting over Wire EDM
Feb 17, 2025 by Rainford Precision
3 min read
The Impact Of Kern Automated Production At WLR Precision Engineering Limited
Dec 6, 2024 by Rainford Precision