The Guide To Avoiding Common Precision Cutting Tool Mistakes
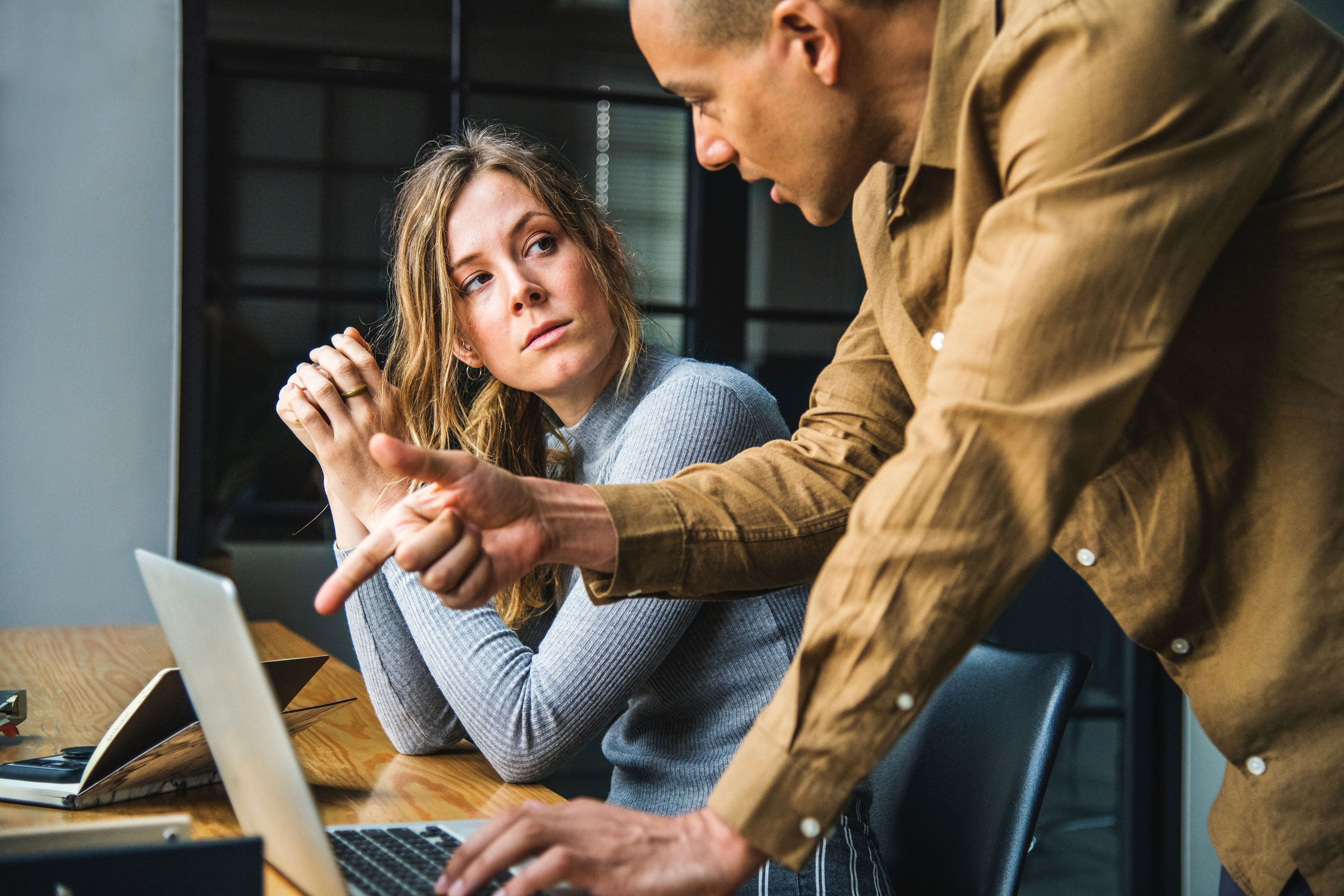
Introduction
In precision machining, accuracy is everything. Even the smallest mistakes can lead to significant setbacks resulting in unplanned downtime, lost production and unexpected costs. Consistent, high-quality workpieces aren’t just the result of having the right equipment, they are produced when operators understand the nuances of how to use that equipment effectively.
This guide delves into the common pitfalls encountered when working with precision cutting tools, how to avoid them and how to get the most out of your equipment.
.webp)
Understanding Cutting Processes
Precision cutting tools are multifaceted, with a plethora of important applications across many different industries. From automotive and engineering to aeronautical and medical, precision cutting tools are used for thousands of highly technical processes where accuracy is paramount.
Turning
In the case of turning the workpiece rotates while the cutting tool remains stationary to create the desired shape which is typically cylindrical in nature. It’s often used to create parts like shafts, bushes and threaded components.
Milling
Simplified, milling involves the application and use of a rotating cutting tool while the workpiece either remains stationary in 3 axis or moves in 4 or 5 axis machining. The milling tool removes material from the workpiece to create shapes, holes, pockets and features.
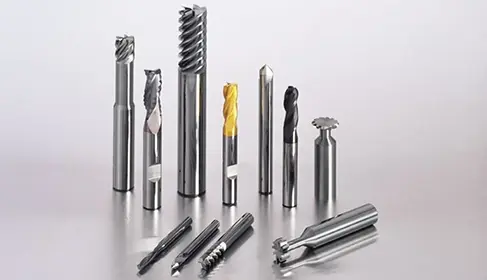
Free Download
The Guide To Avoiding Common Precision Cutting Tool Mistakes
Our free guide offers invaluable advice on avoiding costly cutting tool mistakes and optimising your machining operations.
Download Now
Tapping
This process creates internal threads in a bore, allowing bolts or screws to be fastened securely. A cutting tool with the desired thread size and pitch is advanced into a pre-drilled hole, cutting material away as it goes.
Thread Milling
Like tapping, thread milling is used to create threads in a bore or on the outside of a workpiece. However, thread milling uses a multi-axis CNC machine to move the thread mill along a helical path to form the thread profile rather than the single axis movement used in tapping.
Drilling
Drills are used on the vast majority of components manufactured today and can vary enormously in their diameter and depth capabilities. Rainford stocks hundreds of precision drills that are suitable for a wide variety of applications, which are used to create highly accurate holes where tight tolerances are crucial and precise alignment is required.
.webp?width=1132&height=756&name=V1_JDRGroup_Rainford%20Ebook_1414X2000px_RAP_12.02.25%20(3).webp)
.webp?width=1132&height=1132&name=V1_JDRGroup_Rainford%20Ebook_1414X2000px_RAP_12.02.25%20(4).webp)
Micro-Machining
Micro-machining is a process, tailored towards extremely small components, which uses specialised CNC machines like the Kern Micro or Kern Pyramid Nano, combined with precision cutting tools, to cut and shape materials at the micro level. This is most often used in manufacturing components in watchmaking, micro mechanics, electronics and medical devices, where high precision in the micro scale is necessary. To achieve this, factors such as vibrations, tool alignment, and heat generation must be meticulously controlled, as even minor errors can go undetected at such small scales, resulting in significant consequences.
Reaming
Reaming is a precision tooling process to smooth and/or enlarge the interior of a bore to achieve an extremely accurate diameter and improved surface finish. Reamers are multi-faceted cutting tools, often with six-plus cutting edges arranged around their circumference to allow very small amounts of material to be removed consistently. They’re capable of achieving extremely tight tolerances, ideal for parts where hole size is critical for function and fit such as bushings, bearings and dowel pins.
.webp?width=1132&height=756&name=V1_JDRGroup_Rainford%20Ebook_1414X2000px_RAP_12.02.25%20(5).webp)
.webp?width=1132&height=637&name=V1_JDRGroup_Rainford%20Ebook_1414X2000px_RAP_12.02.25%20(6).webp)
Boring
Boring bars are used to either enlarge and finish the internal diameter of a pre-drilled or cast hole, or to create internal features inside a bore. They refine the hole’s dimension, roundness and surface finish and are used when standard drilling cannot meet a specific size or tolerance requirements. They can improve hole geometry, correcting imperfections left by the previous machining process and are important in applications where smooth contact surfaces are required such as hydraulic cylinders or precision housings where reaming is not necessary.
Download Your Free Copy!
.png)
Our FREE guide, 'The Guide To Avoiding Common Precision Cutting Tool Mistakes,' offers invaluable advice on avoiding costly cutting tool mistakes and optimising your machining operations.
- Eliminate Dimensional Inaccuracies
- Master Speeds & Feeds
- Troubleshoot Cutting Issues
- Extend Tool Life & Reduce Downtime
Identifying Common Mistakes
Precision machining demands exactness, as even minor deviations can lead to significant problems. By understanding and anticipating common mistakes, manufacturers can prevent errors before they occur, ultimately streamlining production and improving efficiency.
Dimensional Inaccuracies
Even the slightest deviation from specified measurements or tolerances can compromise functionality and fit, which is critical in high-precision industries such as medical devices, watchmaking, or aerospace. In the worst-case scenario, such errors could result in a scrapped component. This can happen for various reasons, including tool wear, but it may also stem from machine-related issues such as thermal expansion, improper workholding or toolholding setups, or incorrect speeds and feeds. These factors can lead to vibrations or poor surface finishes on the component.
Surface Finish Issues
This occurs when the final finish doesn’t meet the specifications or desired appearance, causing problems with functionality, wear resistance and aesthetics. It’s typically caused by a combination of factors, including tool wear, tool chatter and vibration, heat generation, material hardness, incorrect tool geometry or environmental changes.
Tool Wear
All tools will inevitably wear out over time, regardless of how well they are maintained. However, this wear and tear can occur much faster if tools are used improperly or for the wrong application, or if regular maintenance and inspections are neglected. Using the wrong tool can lead to poor surface finishes, rapid wear and damaged workpieces. Similarly, a lack of maintenance will decrease precision and increase the risk of tool breakage. A dull tool cutting edge can generate excessive heat which can further damage the tool itself or even the workpiece.
Using The Wrong Speeds And Feeds
The wrong speed and feed can result in excessive tool wear, poor finishes and tool breakages. Both fast and slow speeds and feeds can impact quality and accuracy.
Lack Of Training And Poor Setup
If staff lack the necessary training, it’s all too easy to select the wrong cutting tool, speed or setup, leading to tool misalignment and a poor-quality end product. Without specialised knowledge it’s difficult for operators to troubleshoot and get machines back up and running quickly.
Inadequate Chip Control
Accumulated chips and debris can clog cutting areas, reducing cooling and affecting the workpiece quality. Poor chip control can also lead to tool breakage, potentially resulting in a scrapped component which in turn will drive up production costs. Maintaining effective chip control is essential to keeping operations efficient and costs in check.
.webp)
Preventing Tool Damage
Maintaining your cutting tools is essential to keep them in good working condition to ensure quality and reduce downtime. Here are our top tips for extending tool life:
- Select the right feed rate and cutting speeds.
- Use the right tool for the material. For example with harder materials a carbide or CBN tool will be more suitable.
- Regularly inspect tools for signs of chipping, dull cutting edges and component surface roughness to identify tools which need replacement or resharpening.
- Ensure proper tool alignment and minimise tool overhang.
- Control temperature with coolants and lubricants to reduce heat generated during cutting.
- Implement effective chip control such as chip breakers to cut them into shorter pieces and prevent them interfering in the cutting process.
- Use tools built with anti-vibration features to help stabilise the cutting process.
- Store and handle your tools correctly. Exposure to moisture might not effect the cutting tool but could cause corrosion of the tool holder.
Ensuring Material Quality
You can have the best precision cutting tools in the world but if the materials they’re cutting are not up to scratch you will run into problems.
Always request supplier certification to show the raw materials meet the required standards and work with reputable suppliers who are known for providing consistent quality. Check for visible defects such as cracks or warping upon delivery and use calipers, micrometers and hardness testers to verify basic properties.
Depending on the application and industry you may need to use spectroscopy to analyse the composition, tensile and compression testing to measure the material’s strength and impact testing to determine its hardness.
.webp)
Optimising Cutting Parameters
Getting your cutting parameters right can dramatically reduce tool wear and tear and improve tool life. There are several things you should consider when doing this:
- Material hardness – Harder materials typically require lower cutting speeds and smaller depths of cut to avoid excessive tool wear.
- Thermal conductivity – Materials with low conductivity such as titanium retain heat when being cut so require lower speeds and effective coolants.
- The right cutting tools - Hard materials usually need carbide or CBN cutting tools while softer materials are more suited to high-speed steel, sharp carbide tools or even ceramic tools. With very abrasive materials PCD can be the best option.
- Determine the optimum cutting speed – This should be based upon the manufacturer recommended cutting speeds balanced with tool life. Higher speeds may increase productivity but can also increase tool wear.
- Set the appropriate feed rate – This will depend on the material used, tool geometry and machine’s capabilities.
- Adjust cut depth based on tool and material – Harder materials place more stress on the tool so reduce the depth to cut the load and minimise tool wear. For roughing operations a deeper depth can be used to remove a large amount of material rapidly. For finishing operations, reduce the depth to achieve higher precision and surface finishes.
- Perform test cuts and analyse the results – Even if you think you’ve set everything correctly test the setup before proceeding to full production and make adjustments as necessary.
Troubleshooting Cutting Issues
It’s frustrating when quality isn’t up to scratch but there are things you can do to identify the issue and improve cutting accuracy:
- Excessive tool wear – Reduce cutting speed, use a more wear-resistant tool or coating and improve coolant application.
- Poor surface finish – Replace or re-sharpen the tool, reduce the feed rate, minimise vibrations or adjust tool geometry for better cutting conditions.
- Excessive chatter or vibration – Adjust the feed rate, reduce tool overhang and ensure both the tool and the workpiece are securely clamped.
- Tool breakage – Check the depth of cut is not excessive and reduce as necessary, adjust cutting speed and feed and ensure your feed per tooth is not too high.
- Dimensional inaccuracy – Inspect tools for wear and tear, replace worn tools, ensure machine stability and control heat build-up.
.webp)
Implementing Quality Control
Quality control should be present before you even make a cut to ensure accuracy every step of the way. There are key measures you can take to ensure you consistently achieve precise results.
- Start with thorough inspection and analysis of the raw materials to ensure they meet the specified standards for hardness and composition.
- Next ensure the correct calibration of any CNC machines, lathes and other cutting equipment.
- Implement a regular tool monitoring programme which tracks tool life.
- Consider using real-time sensors to monitor vibration, tool wear and temperature as well as provide instant feedback.
- Employ adaptive control systems or CNC machines which automatically adjust elements such as the feed rate, speed and depth of cut.
Tool Holding
How the cutting tool is held in the spindle of the machine tool can substantially affect the tool life and final surface finish achieved. It’s important it’s aligned properly with the spindle to ensure it follows the intended cutting path accurately. The holder must also be sufficiently rigid to avoid bending or unintentional movement of the tool under cutting forces. Remember.....concentricity is key in ensuring good tool life and reliable results!
Work Holding
Just as the cutting tool holder needs to be sufficient so does the holder or clamps keeping the workpiece in position. Proper workpiece holding will improve dimensional accuracy, surface finish and overall machine efficiency. Vices, clamps, magnetic chucks and custom fixtures all provide varying degrees of stability.
Speeds And Feeds
High cutting speed or tool rotation speed combined with too slow a feed rate can generate excessive heat, which will dull the cutting edges leading to tool deflection. Essentially, you will be rubbing and not cutting efficiently. The knock-on effect is the production of inaccurate parts and a poor surface finish. On the other hand, operating at too low a speed can lead to overloading, excessive chip accumulation in the flutes, and increased strain on the cutter, resulting in premature tool wear and potential breakage.
Optimising your speed based on tool type and material will lead to precise, consistent cuts.
Quality Of Carbide
Many different cutting tools are made from carbide but not all are created equal. At Rainford we only stock the highest quality tools. They may be more expensive to buy initially but their superior quality means they perform more accurately and last far longer when applied correctly. High-quality carbide with a uniform microstructure and optimal blend of tungsten carbide and cobalt binder provides sharp, durable cutting edges that can withstand the forces of machining without chipping or dulling quickly.
Microscope: Advanced Tool Analysis For Enhanced Precision
Rainford Precision leverages the cutting-edge Keyence VHX-970FN digital microscope to deliver a comprehensive tool analysis and consultancy service, free of charge. This service ensures that customers can maximise their tool performance and lifespan through detailed diagnostics and expert recommendations.
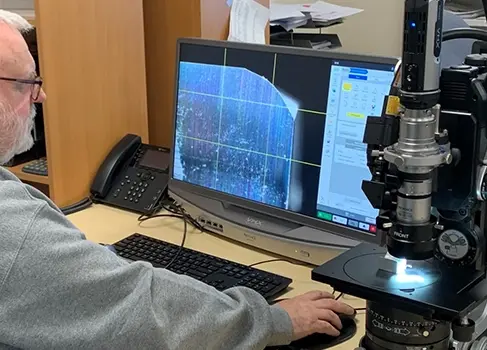
Capabilities of the Keyence VHX-970FN Microscope
The Keyence VHX-970FN microscope offers an impressive magnification range from 20x to 1000x, enabling precise analysis of both standard and micro-tools. This level of detail is particularly crucial for tools with diameters below 0.5 mm, which often present challenges in diagnosing wear or optimisation barriers. The microscope’s advanced imaging capabilities allow Rainford Precision to identify even the smallest defects, ensuring customers achieve optimal tool performance.
Service Process
- Customer Tool Analysis: Customers are invited to send their cutting tools to Rainford Precision for in-depth analysis using the Keyence microscope. A detailed report is generated, diagnosing issues and providing tailored recommendations for improvements.
- Pinpointing Root Causes: The high-resolution imaging enables the identification of specific tool wear characteristics, cutting parameter issues, or tool holding and concentricity problems. By pinpointing these root causes, Rainford Precision helps customers make informed adjustments to their processes.
- Maximised Efficiency: Implementing these recommendations translates to reduced tool wear, enhanced productivity, and significant cost savings.
Services for All Cutting Tool Users
This service is accessible to customers across industries, including aerospace, medical, defence, motorsport, education, nuclear, and watchmaking:
- For Existing Customers: A full diagnostic report is provided, detailing recommendations to optimise tool performance and extend tool life.
- For Potential Customers: Rainford Precision analyses tools (irrespective of the manufacturer) and offers improvement advice. Additionally, customers receive a quote for tool solutions tailored to enhance their processes.
Why Use Our Service?
By combining advanced technology with years of industry expertise, Rainford Precision not only identifies tool issues but also offers actionable solutions to enhance machining outcomes. The service is particularly beneficial for industries in the high-precision and high quantity production areas, where even minor inaccuracies can have significant effects on the cost per component. This commitment to quality and innovation underscores Rainford Precision’s role as a leader in precision tooling optimisation.
Precision Solutions Backed by Expertise and Innovation
Rainford Precision’s long-standing commitment to excellence and innovation has made it a trusted name in precision engineering since its founding in 1991. With over three decades of expertise, our company has continually grown and adapted to meet the needs of a wide range of industries, including aerospace, motorsport, medical, and the nuclear sector. Proudly certified to ISO 9001:2015 standards, we are committed to delivering excellence at every level.
As industries continue to push the boundaries of what is possible, Rainford Precision remains steadfast in its mission to provide tools and services that meet the highest standards of accuracy, reliability, and efficiency. Whether addressing common cutting tool challenges or offering bespoke engineering solutions, Rainford Precision is uniquely positioned to support businesses in achieving their precision manufacturing goals.
For more information on how Rainford Precision can help optimise your machining processes, visit rainfordprecision.com or get in touch with one of our expert team today.